What Are Solid State Relays Used For?
March 29, 2022
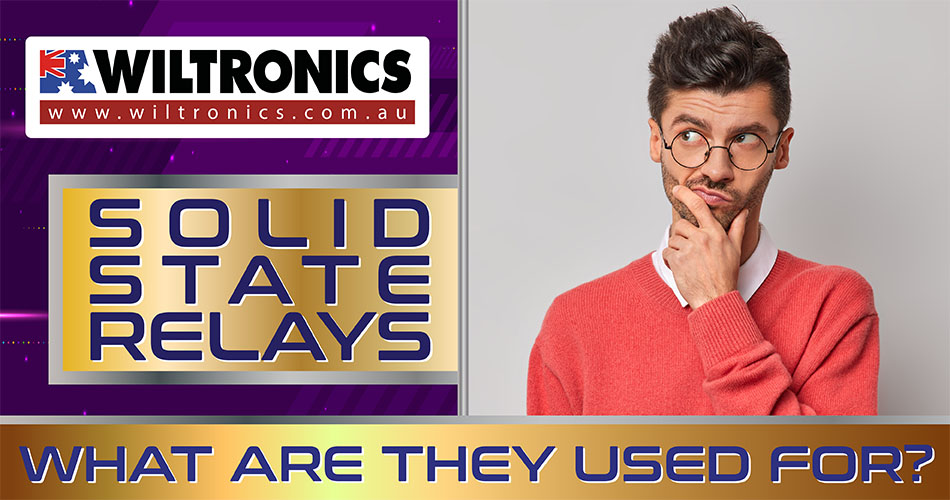
Knowing what solid state relays are will give you an advantage when working with circuits.
Relays are electrically operated switches that use low-power signals to control high-power devices. There are three common types of relays, and one of them is solid-state relays (SSRs).
In this post, we examine what a solid state relay is and understand how it works, its uses and more. Throughout, we prepared a section about solid state vs electromechanical relay.
Read on and see how an SSR can benefit you, and learn which type of relay, in general, suits your needs!
Relays and Their Types
Relays are switching devices that control one circuit by switching contacts. Generally, they automatically close or open a set of contacts between two circuits.
A contact is an electrical circuit component found in switches, connectors, and breakers. Each consists of electrically conductive material, usually metal.
This process is triggered by an electrical input or control signal of some kind. In return, the relay switch moves from an ‘off’ to an ‘on’ position.
The relay closes (or opens) a set of contacts, thus completing (or breaking) the circuit. In most cases, when the relay device is receiving no signal, the contacts are open. This also means that the circuit is effectively incomplete.
A variety of relays are available in the market, but one of the most common types is solid state relays. Others include machine control and electromechanical relays.
Machine control relays
A magnetic coil operates machine control relays. They are heavy-duty, making them ideal for control starters and other industrial components.
Their durability also makes them more expensive than electromechanical and solid state relays.
Electromechanical relays
Also known as an EMR, this type of relay is operated by a magnetic force. It is robust and bigger yet slower than solid state relays.
A typical model consists of heavy-duty frames that support all parts of the relay, such as:
- Coil – creates the electromagnetic field;
- Contacts – closes or opens the circuit;
- Armature – opens and closes the contacts;
- Spring – returns the armature to its original position;
- Yoke – provides a low reluctance path for magnetic flux.
EMR operation time ranges from 5 to 15 ms, which is insufficient for some applications. Further, it contains moving parts, which shorten their lifespan.
But EMRs are available in a wide range of switch figurations. Plus, they are affordable and easy to replace.
Now, for the main part!
Solid State Relays
Short for SSR, solid state relays do not have moving parts. They provide completely electronic switching and do not contain any moving contacts. Moreover, they use the electrical and optical properties of solid-state conductors.
SSRs perform the same on/off and open/close functions as standard relays. A solid state switch does the same but without physical movement within the relay itself.
This switching device ensures there is complete electrical isolation between input and output. When they are switched off, they have high resistance. In contrast, when they are conducting, they have low resistance.
Depending on the model and applications, SSRs can be designed to operate on AC or DC input currents. Common voltages for DC include 5V, 12V and 24V.
And as for AC solid state relays, they are often based around 120V or 240V input. Simply put, SSRs provide a wide range of current depending on the application. This makes them very handy and suitable for most electronic circuits.
SSR Configuration
SSR design includes three main parts:
- Input circuit
- Control circuit
- Output circuit
The input circuit has the same function as the coil in electromechanical relays. It is activated when it senses a voltage higher than the relay’s specified pick-up.
Meanwhile, it is deactivated when the voltage is lower than the minimum dropout. The control component is connected to this relay part.
The coupling between the input and output circuits work in the simplest way. They determine when the output component should be energised or de-energised.
As for the output circuit, it has the same function as the mechanical contacts in EMRs. In short, it switches the load. In every SSRs, there is one output contact.
SSR vs EMR
Solid state and electromechanical relays are similar in their low voltage input. It is electrically isolated from the output that switches and controls a load.
However, electromechanical relays (EMRs) have a limited contact life cycle. They take up a lot of room and have slower switch speeds. this is especially true for large power relays and contactors.
Solid state relays have no such limitations. SSRs, unlike EMRs, have no moving parts to wear out. Thus, there are no contact bounce issues.
Moreover, solid state relays can switch both on and off much faster than mechanical armature can move. There is a zero-voltage turn-on and zero-current turn-off, eliminating electrical noise and transients.
The Benefits of SSRs
1. Ease of design
The circuit board footprint and total volume of SSRs are smaller than EMRs of similar specs. Solid state relays also tend to be lighter by up to 70% than EMRs, depending on the power.
The size and weight of this relay type make it highly desirable for embedded systems. In return, it helps save valuable installation space.
Further, SSR operation is position insensitive. Meaning they are suitable for mounting in either a vertical or horizontal position.
And although SSRs are smaller in size than others, they are no less powerful. Optical coupling completely isolates the circuits of the relay. This eliminates the failure caused by high voltage.
2. Longer lifespan
With SSRs having no moving parts and contacts, there will be no arcing issues or mechanical wear. Because of this, the expected lifespan is 50 times longer than EMRs.
This makes solid state relays an ideal solution for applications that need frequent operation.
3. Low power consumption
SSRs do not need to energise a bulky coil and open and close contacts like others do. They use less power to operate.
The input power of SSRs is enough to drive an optical coupler LED, which consumes very low energy. A solid state relay only needs an input power of microwatts to a few milliwatts.
Meanwhile, EMRs require input power in the range of hundreds of milliwatts to a few watts. See the difference?
4. Fast switching
SSRs provide much faster switching when compared to other relays, especially EMRs. The switch on/off is faster as there are no physical parts to move.
The switching time depends on LED switching on/off time. It responds to a control signal almost instantaneously (less than 100 µs). While the average switching time of EMRs is from 5 to 15 ms.
5. Suitable for harsh environments
Temperature, dust, humidity, vibration and mechanical stress. These can trigger the function and lifespan of relays.
But since SSRs are enclosed in housing, they are well-suited for harsh environment applications. Moreover, SSR operation does not cause sparking.
This makes the relay switch suitable for combustible settings. External magnetic fields also have insignificant effects on SSRs.
The Bottom Line
To understand what a solid state relay (SSR) is, it is important to know the basics first. This includes understanding the standard electromechanical relay – and how these two differ.
We hope this article has given you the key information about solid state relays. When choosing an SSR, feel free to go back here and use this as buying guide.
Speaking of purchasing, make your shopping hassle-free and browse through our SSRs online! We offer a range of SSRs 3-32VDC input – 250vac output. Shop Solid State Relays here.
© Electrotech Brands Pty Ltd 2022
Write a Comment
You must be logged in to post a comment.